JTAGテクニカルニュース <特別編>
BGAの実装不良の有無を見つけるためには、電気的テストである『JTAG/バウンダリスキャン・テスト』が非常に有効です。
高密度実装のためにBGAが生まれた!
従来のリード端子を部品周辺に持つ QFP(Quad Flat Package) や SOP ( System On Package) に代わり、比較的小型で多ピン化を可能としたパッケージとして開発されたのがBGA(Ball Grid Array)です。
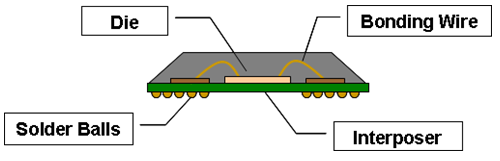
BGAは、本来は次の目的のために開発されたパッケージとなります。
- 従来パッケージに比べ、より高密度実装が可能
- 実装に起因するリペア作業が非常に少ない
- 実装の歩留りが高くなることによって、プリント基板組立のトータルコストを低減できる
しかしながら、BGAは部品実装の品質確認において大きな問題点を抱えているのが現状であり、これには、部品パッケージの構造が少なからず関係しています。
下図は、BGAのバンプ(ボール形状の端子)と基板との接続イメージです。
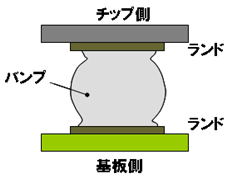
BGA実装には問題がいっぱい?
実装に関する問題としては、基板自体の不良(パターン、スルーホール、ランド不良)の他、実装の際のはんだ不良があります。
実装については、一般的に、リフロー行程において適度な温度プロファイルが設定されていれば、問題が発生するケースは少ないようです。
しかしながら、温度条件が悪い場合、ハンダ溶融が不十分となって、未接続の状態になることがあります。
また、加熱をし過ぎることによってバンプが変形し、隣接する端子間でブリッジが発生したり、ハンダ流れや飛散によるハンダ量不足によって未接続となることがあります。
さらに、温度による基板やパッケージの反り、実装時の部品の位置ズレ等が原因で不良となるケースもあります。BGAの不良の例を図示してみました。
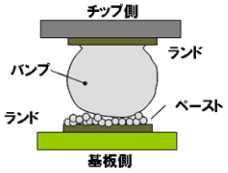
基板側ランドに塗られたペーストが未溶解のために不良となる
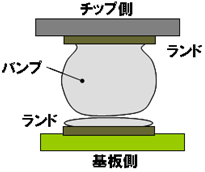
バンプと基板側のランドに塗られたペーストが融合していないために不良が起こる
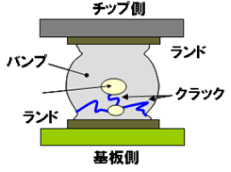
バンプ内の空洞部であるボイド。熱的・機械的ストレスによるクラック(剥離・亀裂)
※ボイドが多い部分には、クラックが発生しやすい。
このようなBGAの実装不良は、外観検査装置やX線装置で見つけることが難しく、また、不良の原因追求のために多くの時間が費やされてしまいます。
とくに極微細クラックなどは、見つけられないケースも多いようです。
いかがでしょうか、BGAの実装の難しさをお分かりいただけたでしょうか?